Concrete is widely used for foundation walls, the perimeter structural walls built on footings that support buildings within the soil below ground level in basement and sub-basement areas. In older buildings, foundations may also be brick or rubble. Rubble or stone is the most porous with wide large mortar joints. Water cannot penetrate through brick as easily as stone, but brick is more porous than concrete.
Stress cracks occur when newly poured concrete hardens and water evaporates causing the concrete to shrink and crack. Cracks also occur from the settlement of the footings into the soil below; from temperature changes that cause expansion and contraction; and from the vibrations of passing traffic.
Water - The Unwelcome
Intruder
Water intrudes because most cracks are full depth, penetrating from the exterior through the interior of the concrete foundation wall. Water from soil saturated from rain or melting snow finds the point of least resistance and enters through the wall into the basement or sub-basement space.
Years of leakage through cracks will compromise the structural integrity of a building. As the concrete deteriorates the steel rebar encased within the concrete rusts and corrodes, causing the concrete to spall.
Mold is another serious consequence. As leaks enter the interior space, it can begin to grow on the sheet rock and other interior finishes.
Conventional Prevention
and Treatment
In newer construction, a waterproofing membrane is sometimes installed on the exterior side of the foundation below ground level. This can prevent water flow if applied properly and backfilled carefully. For older buildings, the tar-type of coating that was applied years ago will have deteriorated.
Excavating from the exterior to install waterproofing membranes in older buildings is not a practical solution in New York City and most urban areas. It is enormously disruptive to tenants, costly, and would often destroy landscaped areas that greatly enhance a building's curb appeal.
French drains are sometimes installed on the interior side of the base of the concrete wall; this involves chopping out trenches through the floor to collect water which then flows to a pit on a lower elevation where it collects again and is pumped out through a sewer main. Many building owners are not pleased to have water intentionally flow into a building.
Grout injection drills holes on the interior then uses materials, mainly polyurethane expanding foams, to fill up cracks and form a curtain membrane on the exterior side of the wall. This method too has drawbacks. Grout inject requires creating more holes on the exterior side which would damage any previously installed waterproofing membrane. Also, since grout expands it will eventually break down and lose its adhesive properties in the presence of water. The steel ports from the interior will corrode when the foam breaks and water begins to intrude again.
The CGI System -
Concrete Gel Injection
The CGI system (Concrete Gel Injection) involves below ground injection waterproofing from the interior side of a building without excavating from the exterior. Since 2004, CGI has successfully stopped water leakage in hundreds of commercial and residential buildings in the N.Y.C. metro area.
CGI injections go only within the depth of the structure. The system drills holes and injects a two component hydrophilic resin that chemically reacts to form a flexible water sealing gel through the process of polymerization.
The two liquid components combined are near the viscosity of water. When the CGI chemical reaction takes place, the gel doesn't expand like urethane foam, it simply occupies the volume of the crack full depth to the exterior side. Also, unlike grout injection, the system doesn't drill all the way to the exterior side which could compromise any previously installed waterproofing membrane. No excavation is needed. This system can also be performed through brick and stone walls and structural vaults.
The CGI system has many benefits:
* It is highly elastic - flexible to vibrations/movements.
* It is less costly than methods requiring major overhauls such as excavation.
* It cleans with water - no cleaning solvents required.
* Little to no odor is produced during and after gel reaction.
* It will not promote growth of fungi, mold, or bacteria.
* CGI is environmentally safe and non-toxic, non-flammable, and non-hazardous.
* Unlike grout, it will not breakdown in the presence of water containing oil, salt and/or sewage.
* The CGI process does not require drilling to the exterior side.
A few of the buildings that have successfully eliminated leaks through the CGI system are NY Presbyterian Hospital/The Helmsley Medical Tower; London Terrace at 435 W. 23rd St.; the GM Building at the Fifth Ave. Apple Store; The New Yorker Hotel; several NYU locations; The Ritz Carlton Hotel; The Time Warner Building at Columbus Circle; The BMW Building; Zankel Hall at Carnegie Hall; and The Bank of America Building at Bryant Park.
George Doukas is the executive vice president of CGI Northeast Inc., Long Island City, N.Y.
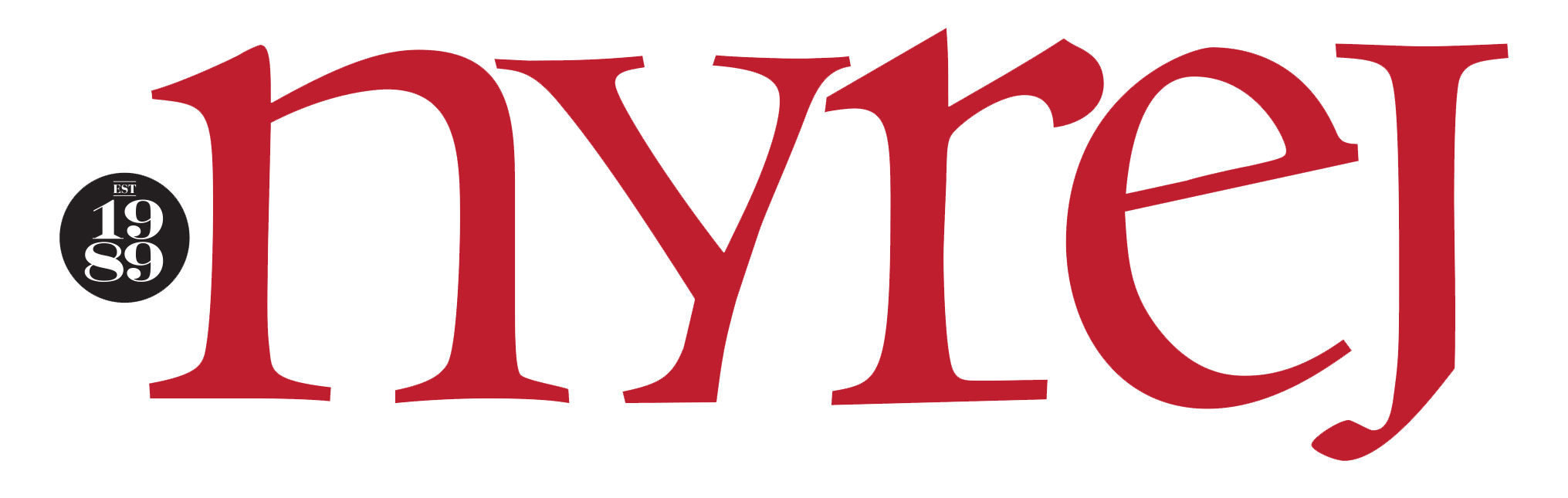
Thanks for Reading!
You've read 3 of your 3 guest articles
Register and get instant unlimited access to all of our articles online.
Sign up is quick, easy, & FREE.
Subscription Options
Sign up is quick, easy, & FREE.
Already have an account? Login here