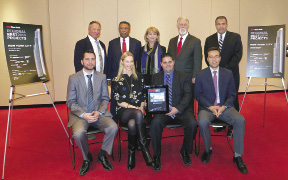
Shown standing (from left) are: Stalco director of field operations James Schuchman, The Liro Group manager Jaio Maraj, BPCA president & COO Shari Hyman, Stalco principal Kevin Harney, and The LiRo Group vice president Frank Franco. Shown seated (from lef
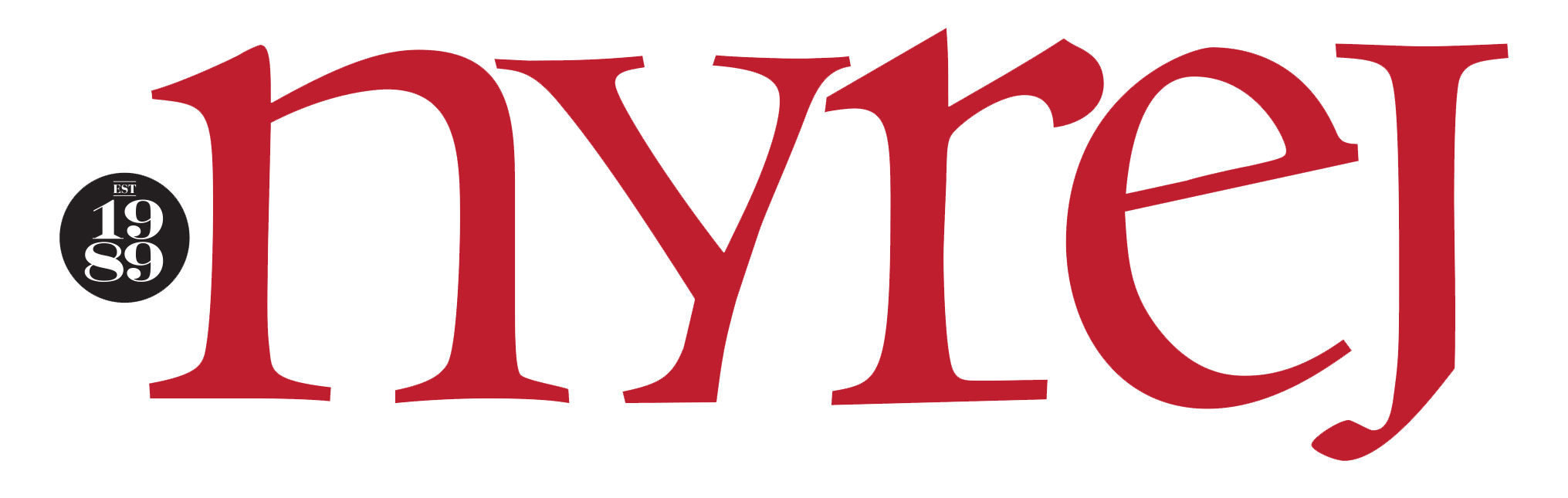
Thanks for Reading!
You've read 3 of your 3 guest articles
Register and get instant unlimited access to all of our articles online.
Sign up is quick, easy, & FREE.
Subscription Options
Sign up is quick, easy, & FREE.
Already have an account? Login here