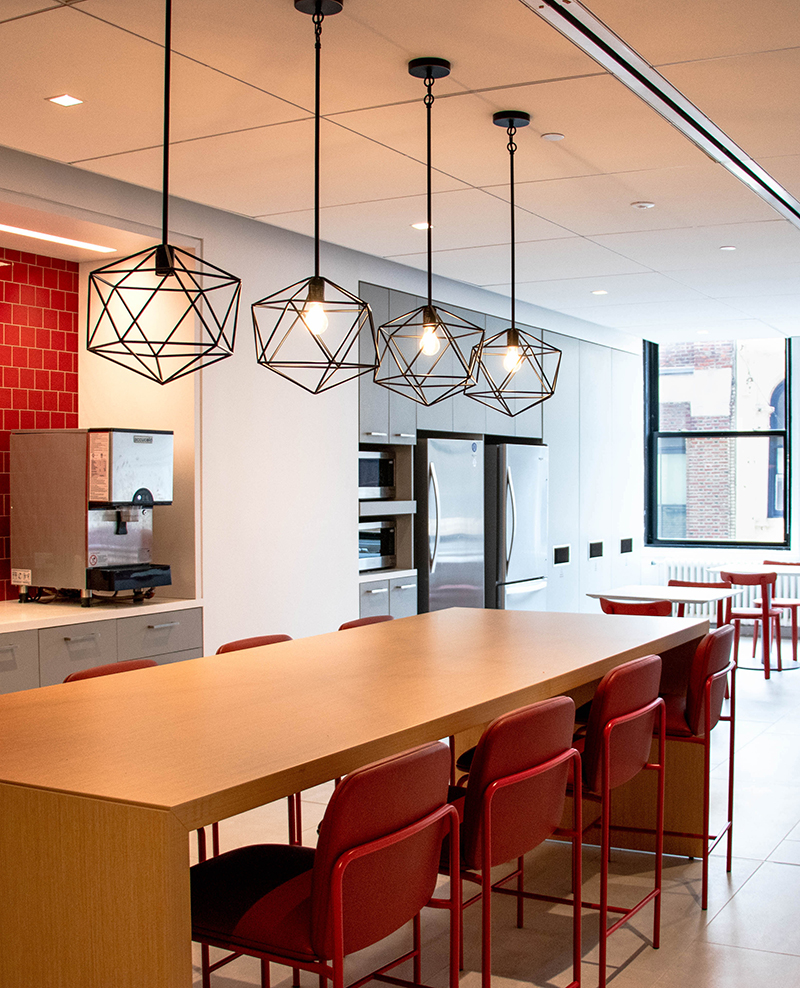
Manhattan, NY Alexander Wolf & Son (AW&S), a family-owned general contracting and construction management firm, in partnership with class A building owner GFP Real Estate, recently completed a groundbreaking $22 million, 200,000 s/f project at 40 Worth St. for Legal Aid Society, the largest social justice law firm in New York City.
Though a veteran in the construction industry since 1905, the project, which comprised expansion and renovation space across six floors built in two 100,000 s/f phases, was one of the firm’s largest and most complex projects to date. As such, the construction firm had to first prove its mettle to its prospective new client, GFP, to win the project.
“Winning GFP’s trust entailed more than a strong interview and competitive pricing,” said AW&S director of operations John Werner. “To assure GFP that we would have complete command of the project, we made introductions to our satisfied clients, conducted project tours, and held in-depth discussions about logistics and how we would approach the coordination of subcontractors.”
“AW&S had a clear vision, strong team and strategy for how they would handle the project,” said GFP head of development, design and construction Scott Beadle. “Once we learned about the firm’s plan for the project, the way they planned to manage all the trades, and the level of care they demonstrated related to the project and GFP, we quickly gained trust in them.”
Winning the project was the first step, however; what followed was an intensive year-long journey to bring the complex project to successful completion.
One of the pivotal early factors in the project’s success, according to AW&S, was the staffing and cohesion of its internal team. The firm’s leadership - AW&S principal Peter Bernstein, director of operations John Werner and director of business development Brian Geller - extended trust to its team of talented field professionals, which included project manager Mark Doherty, assistant project manager Matthew Horne, and superintendent Kenneth Wheeler, empowering them to seamlessly execute and deliver the project with exceptional outcomes.
Moreover, AW&S meticulously curated a strong consortium of external teams, managing contracts with 28 trades and an additional five from the client, among them, leading architecture firm Gensler and engineering specialists firm Robert Derector Associates (RDA). The selection process prioritized subcontractors that shared the goals of transparency, diligence, and addressing challenges promptly and head on to ensure an integrated and synergistic team.
“There was no room for complacency,” said Doherty, the day-to-day onsite project manager. “Each player had to have the same determination as we did.”
With meticulous care and attention to the success of the project through every phase, the team within the first two months anticipated a potential sound transmission issue between the 515 private offices, which had 4,390 linear feet of glass office fronts. Faced with strict sound transmission requirements due to attorney-client confidentiality, AW&S proactively built a full-scale mockup of two private offices - complete with carpets and outlets - to test their Sound Transmission Class (STC) ratings.
The model proved that sound mitigation between offices was insufficient, and found that installing a sound mitigating putty to the back of the electrical boxes on both sides resulted in the required Sound Transmission Class (STC) rating. This level of proactive care and attention averted a potential financial and scheduling disaster.
AW&S was able to apply this same meticulous care and diligence throughout the project’s duration by maintaining an onsite field office from where the team worked and held daily meetings to review status, objectives and forecasts. The approach enabled AW&S to stay in close command of the site, workflow, people, information and materials so that the team could anticipate and address problems at once.
“Any questions or concerns that would come up - whether about an electrical conduit or sprinkler run - we were able to step out of the field office and immediately assess and solve the issue,” said Doherty. “One of the key factors in keeping this fast-paced project moving forward on schedule was our onsite presence and ability to get quick sign offs from the GFP team who also had people in the building.”
Furthermore, AW&S maintained a specific and precise accounting of weekly project milestones in an effort to eliminate guesswork and misunderstandings. The team detailed their expectations, which could be as precise as ‘hang 87 light bulbs in a specific area by a specific date’, for example - on massive drawings outside the field office. For offsite trades, such as cabinet makers, the team required weekly updates with photographic proof of progress. As a result of this deep level of oversight and early coordination, AW&S was able to hit all of its construction deadlines in phase one.
“Rather than pushing subcontractors toward the finish line, we pulled from the front, leading the charge,” said Werner, who noted that subcontractors praised the project’s efficiency, leadership, organization and positive collaborations. “We knew where we needed to go and how to lead the way, so we set the tone, gave everyone a plan, and secured the results we wanted for the client.”
Another critical path for this project was the use of technology to support daily transparent communication with GFP that would allow for immediate feedback from the ownership to ensure that issues were being handled immediately rather than at a later stage of the project.
In addition to the construction management program Procore that provided a communication hub for all stakeholders, AW&S utilized a reality capture and AI-powered analytics program for builders, OpenSpace, that kept visual tabs on the project from existing conditions to real-time status.
Weekly reports comprising an interactive floor plan with approximately 50 360-degree photos – which could capture if the ceiling dimensions were correct or the outlets were in the right spot – were sent to the owners, architects and engineers as a means of monitoring the job site and holding the construction team accountable. The technology streamlined the inspection and punch list process because issues were responded to immediately.
“I couldn’t be more proud of each and every person within our firm that contributed to this project. It was handled with precision, efficiency and energy at all levels. The planning, organization and hard work that went into the project brought out the best in our team and the subcontractors we assembled. That we delivered this project on schedule with minimal change orders is due to these collective efforts. In short, our team knocked it out of the park,” said Bernstein, who noted that GFP has since become one of the firm’s repeat clients, awarding AW&S with three additional projects: 515 Madison, 230 Fifth and 10 Astor Place.
Beadle said “Our initial partnership with Alexander Wolf & Son on a significant and intricate project left us thoroughly impressed. They were quick to assure us of their competence, and then proved their professionalism throughout the project’s duration. Their performance exceeded our expectations, marking a promising start to our collaboration.”
For more information, visit www.awolfandson.com.