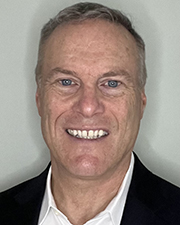
New York City is a clear leader in sustainability. Thanks to very aggressive green building requirements and targets, it is well ahead of most other U.S. cities in this regard.
One reason for that success is the emphasis on supplementary cementitious materials, such as slag, that replace Portland cement in concrete mixes used throughout The Big Apple. These materials provide dramatic reductions in a building’s carbon footprint. Slag, ground granulated blast-furnace slag specifically, has been used as a preferred product in the construction of some of the largest and tallest buildings in the metro New York market…including the Central Park Tower in Midtown Manhattan.
This supertall skyscraper, one of a handful of “Pencil-Towers” around the globe, is the tallest primarily residential building in the world at 1,550 ft. in height or 136 floors above ground. Founded by the Extell Development Company, the tower includes a 28-ft. cantilevered section that starts at 300 ft. above ground, over an adjacent building, and reaches up 1,200 ft. above.
The construction manager for the project was Lendlease and the concrete contractor was Pinnacle Industries. Constructing this unique structure required seven years and 100,000 cubic yards of high performance concrete from Empire Transit Mix. Following New York City’s strict green building protocol resulted in replacing approximately 40% of the concrete’s portland cement with slag provided by Heidelberg Materials. The use of slag resulted in an emission reduction of around 15,000 U.S. tons of CO2.
Recovered and Reused
Slag cement is commonly found in ready-mixed concrete, precast concrete, masonry, soil cement and high temperature resistant building products. It is a byproduct of the steel manufacturing process and is formed when molten slag is diverted from the iron blast furnace then quenched to produce glassy granules that yield desired reactive cementitious characteristics when ground to cement fineness. Once ground to the desired fineness, it is stored and shipped to suppliers throughout the U.S. for use in concrete.
The Environmental Protection Agency classifies slag cement as a “recovered” product under the Resource Conservation Recovery Act (RCRA) and has issued a procurement guideline requiring its specification on most federally funded projects.
Slag can be used as a separate cementitious component or as part of a blended cement. It’s highly advantageous for the New York City metro commercial construction market because of its lower carbon footprint—but also its ready availability and impressive performance characteristics.
Pumps and Pours
Beyond its sustainable advantage, slag cement proved ideal for the Central Park Tower’s mass concrete foundation pours which were 12 ft. thick. The low heat of hydration of slag cement keeps the temperature of the concrete (caused by the chemical reaction of the cementitious material) during pours down, thus reducing the chance of cracks.
Another critical performance requirement was pumpability—or the ease of pushing the concrete mix hundreds of feet in the air—while still achieving a high compressive strength. Slag worked very well as part of the high-performance mix required in this scenario. The overall concrete mix has a compressive strength of 16,000 psi which was necessary to meet the structural design requirements of this unique building.
The Central Park Tower won the 2021 Slag Cement Association’s Sustainable Concrete Award Category for Innovative Applications. This award recognizes projects that used slag cement in the solution to address challenging jobsite conditions and features how slag cement is a key lever in lowering the embodied carbon footprint of concrete.
Dominic Jampo is a specialty products manager, northeast region for Heidelberg Materials, Camden, N.J.