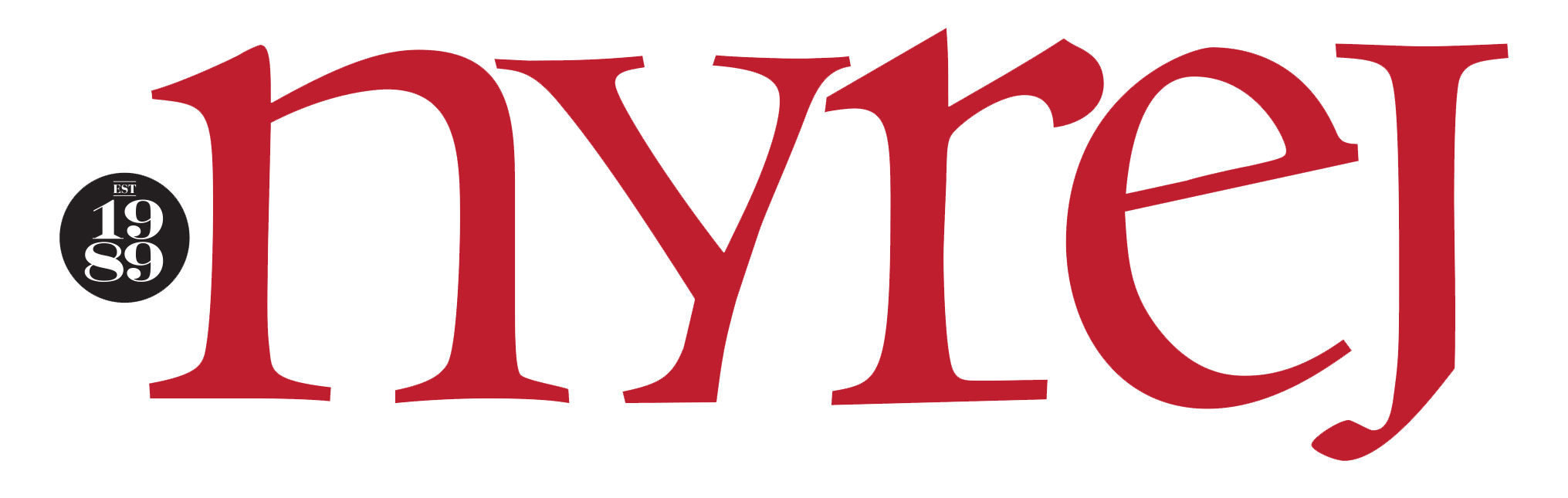
January 12, 2015 -
Design / Build
The leadership, faculty, and students of the Vaughn College of Aeronautics and Technology and the project team of Ensign Engineering, Stalco Construction, and John Ciardullo Associates celebrated the completion of a multi-phase expansion, renovation, and sound abatement project at the college's main campus.
The gala event, led by the college's president Dr. Sharon DeVivo, marked the end of a three-year project that has completely transformed the main campus of the 82-year old private institution into a cutting edge engineering and technology education hub for more than 1,700 students.
The two-day celebrations culminated in the official installation of Dr. DeVivo as the seventh president and the first female leader in the college's history.
"The Vaughn College's diverse population of students includes many first-generation Americans and first-generation college students. Our institution seeks to provide an engaging educational experience for every student, which supports them in their pursuit of a degree as well as lifelong learning," said DeVivo. "The completely upgraded educational and administrative facilities allow us to provide unparalleled service to our students and attract top faculty members, while incorporating the most advanced instructional technology and methods into our programs. I would like to thank the project team of Ensign Engineering, Stalco, and John Ciardullo Associates for their commitment, creativity, and expertise, which made this complex project a reality," she said.
According to Regina Gallagher Marengo, P.E., president of construction manager Ensign Engineering, who managed the renovation, "The nearly $40 million project equipped Vaughn College with expanded and renovated educational and technical facilities; new physics, mechanical, structural, and materials testing laboratories; new public spaces; a new, two-story library and teaching and learning center; upgraded building systems; and the robust sound insulation necessary for a college located only 200 ft. from one of LaGuardia Airport's runways."
The renovations were financed from two sources. Vaughn received grant funds totaling approximately $32 million from the Federal Aviation Administration (FAA) and The Port Authority of New York and New Jersey (PANYNJ) to soundproof the building. In addition to grant financing, Vaughn invested $7 million from its own funds. The project's design was completed in 2009. Construction began in 2011.
Located at 86-01 23rd Ave. in East Elmhurst, N.Y., the project called for the installation of building envelope sound insulation, renovations, re-programming, and building system upgrades to all campus components undergoing renovations. This included the main, one-story structure originally built in 1940; the 1983 classroom building; and a two-story classroom building and a hangar with a 65-foot observation tower, both of which were built in 1997. Two buildings that are not being renovated are the residence hall, which was constructed with sufficient acoustical insulation, and the engine-testing building, where the noise protection is provided individually.
Vaughn College was originally established in 1932 in Newark, N.J. and moved to its current location in 1941. The Queens, site provided easy access to LaGuardia Airport, which is situated across the Grand Central Parkway. Continued expansion of the airport resulted in one of its new runways terminating just 200 feet away from the school, which, along with low-flying airplanes, increased the noise level to the point of interfering with educational activities.
The design and construction team included Ensign Engineering, which served as construction manager; architect John Ciardullo Associates; general contractor Stalco Construction, civil engineer Langan Engineering and Environmental Services; mechanical, electrical and plumbing (MEP) engineer DVL Consulting Engineers; and acoustical consultant Peter George Associates. In addition, Graf & Lewent Architects designed several interior spaces within the renovated main building.
Project Challenges
"One of the primary challenges was the necessity to perform a multi-phase construction project while keeping the school fully operational," said Marengo. "The solution to this challenge was phasing the project through careful planning, extensive safety measures, and the creation of swing spaces."
"The project challenges also included improving the internal layout of the campus and revising the design of staff and faculty offices," added Michael Daly, Vaughn College associate vice president for facilities and college services. "The original administrative offices were located at a significant distance from the main lobby and entrance, which was inconvenient to users and campus visitors. The faculty offices were designed as an open space cubicle area that didn't provide the necessary privacy for meetings between students and teachers. The new admissions, financial aid, and student accounts departments are situated near the main entrance, and new faculty offices offer privacy during meetings."
Swing spaces were created inside the school's buildings and off campus. They included an area that previously served as a library as well as facility offices six blocks away. Planning interior renovations in sections and utilizing swing spaces, allowed the college to move students from areas planned for renovations to sections where renovations had been completed.
The construction team also held weekly meetings with key members of the school's administration and faculty to determine upcoming construction schedules and ensure sufficient spaces for educational activities. Close collaboration and a positive and supportive team atmosphere on the project allowed construction to proceed quickly while minimizing disruptions to the school's daily activities.
Safety within the continuously occupied college was the main concern of the project team. Ensign carefully planned emergency egresses for all interior spaces where building activities were taking place. Temporary fencing and dust barriers around construction areas protected the air quality inside the college buildings. The team also erected protective fencing around the exterior construction zone. All construction activities were closely coordinated with Vaughn's facility management personnel.
Planning construction of the roofs was also a challenge because of FAA height restrictions in close vicinity of airports, which prevented the utilization of temporary roofs above work areas. The solution was to construct some of the new acoustical roofs above existing roofs without removing the original ones, and, in other sections, by scheduling removal in small sections, which made openings easier to protect from elements, without erecting large temporary roofing.
Design and Construction
The initial design work focused on providing sound insulation through revisions to the campus buildings' exterior envelope, including the roofs, walls, and windows. Due to the extent of the roof construction, the project also had to include extensive revisions to the HVAC and MEP infrastructure, as well as related interior construction work beneath the roofs. The college utilized the necessity to perform extensive interior work related to sound insulation as an opportunity to upgrade its educational facilities and improve interior layout and functionality.
The main, 29,000 s/f. building features a lightweight steel structure and brick infill walls. It underwent limited renovations and repairs over the years, but has remained mostly unchanged for 70 years. The building consists of the central main section and two small sections on its sides. In addition to the building undergoing renovations, the triangular campus site also has a dormitory and an "apron," or short runway section for parked airplanes, which were not a part of the renovations.
According to Marengo, "The project was originally divided into 11 phases. However, we reduced the number of phases to six through improved logistical planning in order to reduce the project's schedule. Phase I included an addition of a new atrium lobby and MEP room. Phases II and III included renovations to the older sections of the campus. Phase IV included a section of the main building and conversion of the old library into offices and classrooms. Phases V and VI called for a renovation and upgrades to the section originally built in the 1990s, including new flight simulator and air traffic control simulator rooms."
Roof Design and Construction
All of the renovations included complete redevelopment of the roofs to mitigate sound. The MEP addition is structurally separated from the main building for sound insulation purposes as well.
Typical sound insulation solutions require air spaces. However because airplane engine noise is mostly high-energy and low-frequency, high-mass barriers provide the best insulation. The noise mitigation program for the college included sound insulation of the buildings' envelopes, including roof, walls and windows, as well as HVAC systems.
The roof redesign included either removal of the pre-existing roof and construction of new heavy concrete roof with an air space to insulate against vibration, or addition of new concrete roofs above remaining original roofs. The latter solution allowed the team to accelerate construction and alleviate the need for complex temporary rain protection measures on large areas of roofs undergoing renovations.
The design, developed by John Ciardullo Associates, not only provides sound mitigation, but also visually unifies a campus constructed over a period of 70 years.
The original main building featured brick walls with a band of windows providing light and ventilation. The roof was a gypsum material with girder beams and steel purlins serving as the original roof's structural system. The girder beams were fabricated from steel and the purlins were made from recycled steel from Newark Streetcar rails.
In the sections where the roof was completely replaced, such as on the main building, the lightweight gypsum material was replaced with normal weight concrete and four-inch composite concrete slabs. The designers added Nelson sheer studs on top of existing structures to create a composite slab to increase the strength of the existing roof's steel frame. In addition, the strength of some columns and beams was increased by using additional steel plating. Then, a two-inch rubber EAFM sloping slab system was spread out two feet on center to provide insulation against vibrations. On top of the rubber EAFM sloping slab system, a four-inch acoustical slab was built using regular weight concrete on half-inch plywood to absorb airplane engine noise and vibrations.
The rubber EAFM sloping slab system is by Mason Industries, and includes two-inch load-dynamic stiffness bridge bearing rubber pads. The rubber slabs are placed on top of the structural roof slabs to provide insulation against vibration. On top of the roofs is a structural slab, topped by rubber pads, then covered by half-inch plywood followed by a four-inch acoustical slab that absorbs the low-frequency from airplane engines.
Stub-ups (steel elements added to the existing steel structure) were added in buildings where the original roofing was left in place to protect the interiors during construction. They were used to elevate the new acoustical roof above the existing roof for added sound insulation. Once the stub-ups were in place, the builders could add a new structural steel deck above the existing roof. The new deck consisted of a corrugated metal deck with sheer studs that were welded to the deck and then embedded in concrete poured over the entire metal deck and other structural slabs. The stub-ups are high enough to provide the required air gap between the new concrete roof and the pre-existing roof.
The hangar building's curved roof originally featured a metal deck. Consequently, the noise and vibration solution for the hangar building's roof included a composite concrete slab with Nelson studs on existing beams and girders. Then, a seven-inch structural concrete slab with reinforcing rebar was added with a shotcrete application method. Shotcrete is concrete conveyed through a hose and pneumatically projected at high velocity onto a surface. Shotcrete undergoes placement and compaction at the same time due to the force with which it is projected from the nozzle. It is often utilized to create vertical, curved or irregularly shaped surfaces, such as the curved roof of the hangar.
The hangar's structural slab has embedded curbs to support the three-inch acoustical concrete slab, which is held in place using curbs. The curbs also feature two-inch rubber pads and continuous rubber insulation along the perimeter of the floating roof sections of the hangar building. The curbs here are five-inches high. Acoustical slabs were installed on half-inch plywood sheeting on top of rubber pads. The roofing system also incorporates PVC vapor barriers to prevent moisture infiltration.
Furthermore, because the roof is curved, the half-inch plywood sheeting is composed of two quarter-inch plywood sheets banded together to match the curvature of the roof. These quarter-inch plywood sheets proved easier to band separately than using single half-inch plywood sheeting.
In addition, the original metal deck serves as a form deck for the new structural slab. Basically, the renovation used the existing metal roof as a form deck and rebar was installed on the metal deck.
On all renovated roofs, the team installed a TPO-type asphalt finish with a granulated surface and later painted them with reflective paint for energy efficiency.
Walls and Windows
Older steel-framed buildings, including the main structure, had been composed of yellow brick infill. The renovation repointed and repaired the brick, and where necessary, replaced it with masonry blocks. These exterior walls were added on top of the existing walls and featured acoustical properties.
The new exterior wall system features metal paneling on the outside to match the architecture of the 1997 building. However, some of the existing brick wall was left exposed to reflect the history of the building. The size and number of windows were also reduced. Openings were filled in with masonry blocks and smaller windows were installed to reduce noise penetration.
The new wall system features an isolated acoustical gypsum wall assembly that consists of acoustical rubber isolation clips attached to the brick wall. The gypsum sections have a mass that is twice that of a regular gypsum sheet wall. The exterior of the gypsum sheet walls feature two layers of 5.8-inch-thick exterior gypsum board sheeting installed on three-eighths-inch and five-eighths-inch isolated steel studs. Steel studs were attached to acoustical rubber clips.
The exterior walls feature three kinds of metal panels: quarter-inch composite aluminum panels around the windows; 3.5-inch-thick horizontal Centria MRI 36 metal panels; and two-inch-thick Centria Slab Metal Panel with an architectural accent around the west end of the building, which is visible from the nearby highway and the airport. In the main building, the new windows feature tinted Wausau Triple-Glazed Airspaced Windows.
The project also includes improvements to the 1997 building. These improvements include metal panels on metal stud exterior walls and new interior walls for improved acoustical performance. This building also features new acoustical windows, which were installed in the bridge window openings. The new walls feature 3.5-inch steel studs, half-inch rubber clips, and double-sheet drywall that consists of two 5.8-inch sheets. The 1997 building also includes a three-story classroom section, a one-story laboratory structure located on the perimeter of the hangar building and the hangar building itself.
Mechanical System
The design of the mechanical systems played a critical role in the sound mitigation process. Due to the size of the main building, construction of a central HVAC system proved impractical. The solution was a design in which the HVAC system was installed in sections. Any roof or exterior wall penetrations for ductwork and piping had to be well insulated. All of the HVAC ductwork that passes through the roof features acoustical duct silencers. All ducts within 20 ft. of a roof penetration had to be insulated with two layers of gypsum board that serves as acoustical insulation. All of the HVAC ductwork was separated from the school's structures to prevent any transfer of vibrations. In addition, the ducts are suspended on either acoustical rubber handles or screens. And, all of the ductwork is lined internally using sound-suppression material.