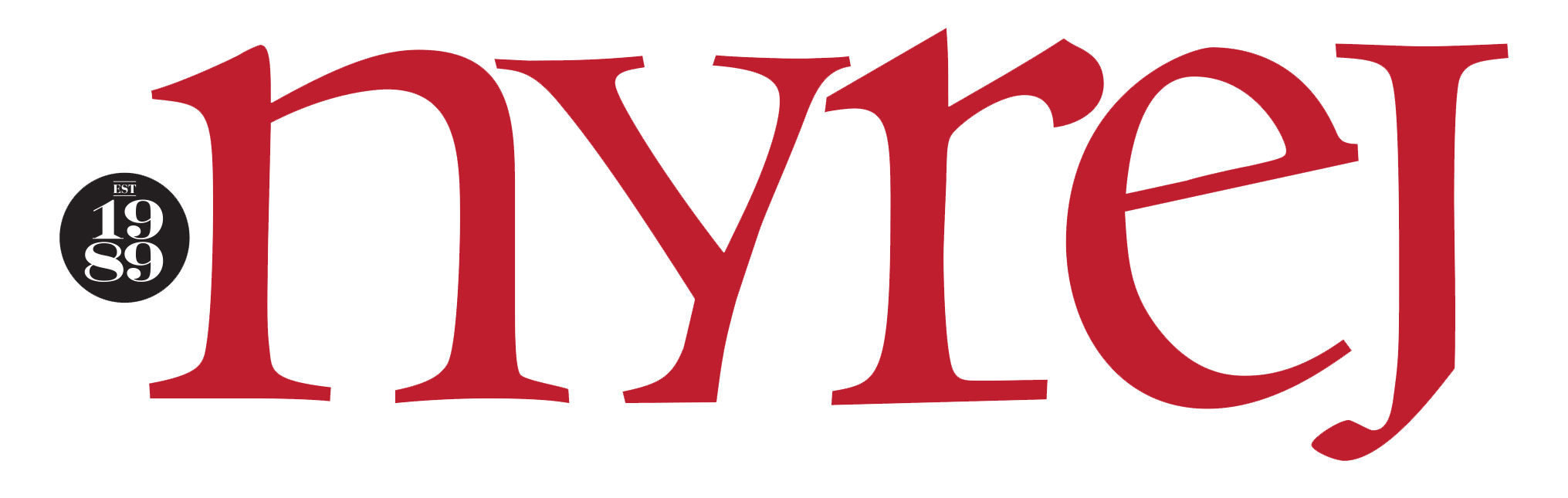
May 09, 2011 -
Design / Build
There are hundreds of thousands of mid and high-rise residential buildings throughout the country with low-sloped (flat) membrane and built-up roof coverings. Effective maintenance is essential to maintain and extend the useful life of such systems.
Capital Reserve Analyses provide anticipated funding for the full replacement of capital items (common elements); however, these analyses typically do not provide detailed recommendations regarding extending the useful life of reserved items. Detailed steps regarding repairs and preventive measures for extending the useful life of items can be established in a Preventive Maintenance Program (PMP). Such steps can increase the useful life of many common elements, therefore reducing reserve requirements. Preventive Maintenance for low sloped roof systems should be included in these recommendations.
By having periodic inspections of the roof system conducted by trained individuals, an owner or manager can plan for needed repair, replacement and retrofitting prior to the occurrence of larger problems. Not only does this planning ensure that the owner or manager has the proper funding in their budget for improvements each year, but it also greatly decreases the chance of catastrophic events caused by severe storms, material failures, and/or wearing deterioration.
There are a number of key points an owner or manager should keep in mind while considering when to implement spending for preventive maintenance:
Relative Value
Evaluating the relative value of spending minimal monies today to avoid large expenditures tomorrow is the fundamental rationale behind a Roof Asset Management Program (RAMP). Deferring regular roof maintenance may cause premature failure of the roof system and may increase the life-cycle cost. Regular, formalized, maintenance will extend the roof life and lower life-cycle cost. A RAMP can be made part of the overall PMP.
Potential for Extended Damage
Often the substrates (decking and rigid insulation) below a low slope roofing system can sustain costly damage when moisture is trapped under the roof covering. Such damage can increase the cost of roof replacement from 50% to over 100%.
Qualified engineering consultants can detect invisible moisture buildup through a variety of testing methods. Such testing should be included as a part of a PMP or roof study. Common testing methods include infrared and electrical capacitance.
Detecting and repairing isolated problems today can eliminate substantial costs down the road.
Professional Consultation
The implementation of the PMP should be under the direction of a qualified professional engineer. Many contractors provide services regarding preventive maintenance; however, by implementing the Preventive Maintenance Program inspections along with normal reserve funding, the professional engineer can better allocate funding, useful lives and obtain more thorough, unbiased, insight regarding the existing conditions of the roofing system. The professional engineering inspections should include additional common element inspections, beyond that of the roofing system. The inspections and analysis will allow for the optimum allocation of the overall funding for the property.
The professional engineer (as opposed to a roofing contractor) does not represent any particular manufacturer or product. As such, a more unbiased opinion can be rendered regarding products, costs, etc. Additionally, many manufacturers' warranties are only valid if a maintenance program has been followed.
A comprehensive PMP including a RAMP is a proactive program which should include qualified inspections on a regular basis. Cursory inspections should be performed in the fall to be sure that the roof is in good condition before the severe winter weather sets in and, in the spring, a more comprehensive inspection to identify maintenance and repair items should be performed.
Roofing is perhaps one of the most important components on a building with respect to weather resistance. With the combined effects of weather, gravity, humidity and heat, the roof must ensure a water tight enclosure that will divert water to its proper destination at ground level. Without proper attention to detail, the roof will be subject to the effects of mother nature. Professionals offer a variety of methods to test for conditions, such as moisture buildup, that not only affect the life of the roof covering but also may decrease the R-value of the insulation, resulting in increased energy consumption of the building.
The ideal time to begin a RAMP is prior to the installation of a roof system. Even toward the end of the useful life of the roof system, preventive maintenance and planning can help an owner or manager carefully plan and budget for replacement. To prolong the life of an existing roof system (or any common element), it is essential to plan economically and set up a Preventive Maintenance Program. By planning today, an owner can extend the useful life of the roof system or other common element which will economically benefit the owner, its reserve funding and improve the property value by eliminating problems through proactive measures.
William Pyznar, P.E., is principal for The Falcon Group, Bridgewater, N.J.