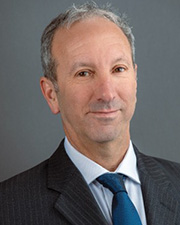
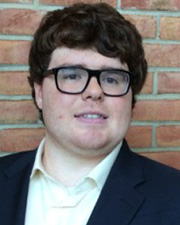
Starting in 2011, New York City Department of Environmental Protection began passing laws banning the use of No. 4 and No. 6 heating oil in New York City (NYC), phasing out the use altogether by 2030. As a result, building owners and managers find themselves having to decide how to keep their buildings heated without using No. 4 or No. 6 heating oil. While many heating systems can convert from No. 4 or No. 6 heating oil to the cleaner No. 2 heating oil, the process can procure high costs, regulatory complications, and in some cases, significant environmental contamination.
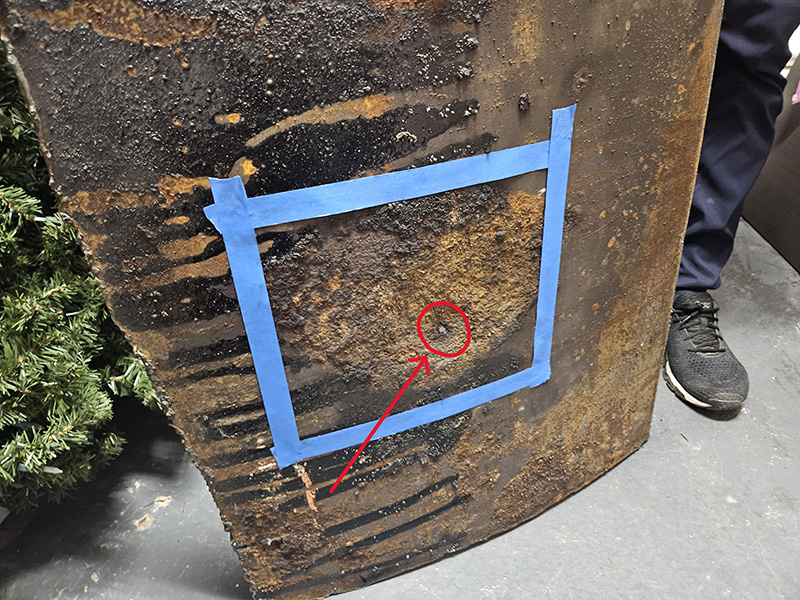
A typical heating system conversion consists of a tank tightness test and a deep cleaning of the tank and associated supply and return lines. NYC law requires a NYC Department of Buildings work permit and updating of the boiler information with the NYC Department of Environmental Registration. The cost for a certified tightness test and tank cleaning often exceeds $5,000. In addition to the tank tightness test and cleaning, the associated NYC fees needing to be paid and regulatory hurdles can be difficult to navigate. A potentially frightening further complication and costly result of a conversion to No. 2 heating oil comes into play where the tank passes the tightness test with an undetectable hole or holes in the tank. By their nature, No. 4 and No. 6 heating oils are thick and can effectively seal a hole in the tank. However, if these holes are undetected and the tank is filled with No. 2 heating oil, the thinner oil can dissolve the plug of heavier oil, causing a leak to occur. We have been called in to deal with this exact issue on multiple sites within NYC, with the leaks requiring hundreds of thousands of dollars to be spent on remediation, testing and tank replacement. With this in mind, we do not recommend the conversion of an existing tank, but rather recommend the replacement with a new tank prior to filling it with No. 2 heating oil.
Converting from heating oil to natural gas is another option, although this comes with its own challenges. The cost often exceeds the cost of conversion to cleaner oil by several thousands of dollars, combined with the lack of available connections in some areas and moratoriums on new hookups in others, due to a lack of natural gas supply. Oftentimes, conversion to natural gas requires a complete replacement of a building’s heating system; a challenge in older buildings and another added layer of expense.
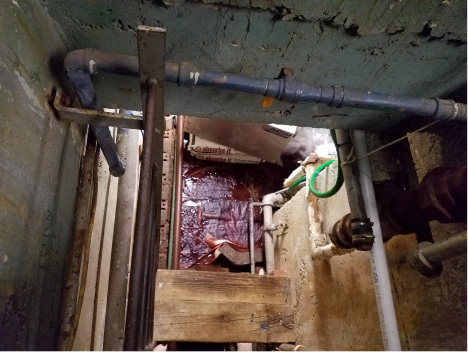
an a leaking tank at an adjoining building.
Given the complex regulatory environment and the rising costs of conversion, building owners and managers who already face challenges in the current competitive and inflationary environment may find themselves balking at the costs of converting. These economic conditions put pressure on tank contractors to cut corners so that they can perform the work at a reduced rate. This leads to a number of issues including spills and leaks, which can result in expensive remedial cleanup, and New York City Department of Environmental Protection (NYCDEP) and New York State Department of Environmental Conservation (NYSDEC) penalties. This issue also affects prospective developers, as the Comprehensive Environmental Response, Compensation and Liability Act (CERCLA) places liability on the owner of a property, regardless of when a spill, leak, or violation took place. Real estate transactions may fall through or lengthy negotiation periods may ensue for an agreement to be made regarding whether the buyer or the seller will pay for the conversion. These regulations, while environmentally sound, prove burdensome, especially for small business owners who do not have any experience with the current law, and process regarding due diligence and risk assumption.
Scott Yanuck, P.G., a member of IREON, is president/owner and Nicholas Kideris is a geologist with Laurel Environmental Geosciences, DPC and ASR Environmental Geosciences, Huntington Station, NY.