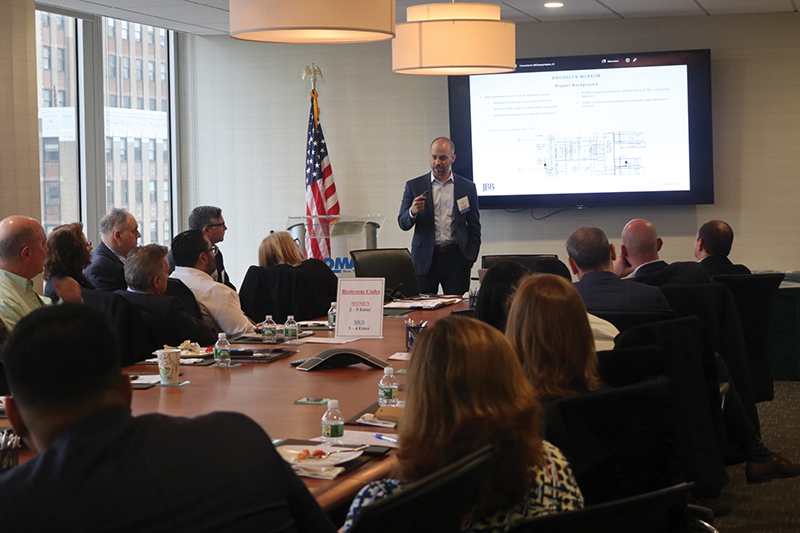
New York, NY The monthly BOMA New York Lunch and Learn series continued to bat 1,000 – with a sellout crowd – as a trio of engineers from Jaros, Baum & Bolles (JB&B) presented three case studies in order to discuss how to best approach infrastructure upgrades and building renovations. Brendan Weiden, partner; Chris Horch, associate partner; and Ryan Lean, associate partner, seamlessly passed the mic and impressed the room of owners and operators with compelling facts and new data.
Prior to diving into the presentation, the JB&B trio reminded the room to be cognizant that times have changed. We need to recognize that workplace strategies have shifted, comply with new energy codes and appreciate that loads are going down. Fifty years ago, we were managing four-watts per s/f. Today, that same load is down to under one-watt per s/f.
Complete Building Renovation
The first case study was of the Ford Foundation Building – a commercial building in the UN District, developed in 1968. Weiden applauded the asset, saying that every piece of the building was custom made, designed with purpose and developed with high quality initial construction. Nonetheless, the COR-TEN steel, brown granite 51-year old landmark was operating inefficiently and was in need of a comprehensive building renovation.
The Ford Foundation Building was developed with a clean roof, placing all mechanicals in the basement. As infrastructure replacements for the building were considered, the engineering team also had to determine how to allow new cooling towers and other equipment to breathe. Another interesting challenge with this building is the “super grid” ceilings. Floor to ceiling heights are 9’8”, with only 3” of space above construction. Therefore, the ceiling is extremely congested. Fortunately, there were beam cuts throughout and all were reused. A full building upgrade is extensive and costly. The following are a few examples that Brendan presented as he showcased the renovation in a nutshell.
The three new cooling towers now breathe through a snorkel to the top of the building, 12-stories up and out. The entire chilled water plant was replaced with new chillers including a 100-ton modular chiller with heat recovery to allow for portions of the building to run 24 hours a day. The dual-dock HVAC system was replaced with a direct outside air system –aka DOAS. A new atrium exhaust system was installed.
The custom light fixtures were removed, refurbished, stripped the incandescent and installed clean tech LEDs. The manual light switches were replaced with automatic light sensors to track occupancy and time of day. Low-flow plumbing fixtures were installed. The building applied for a LEED Platinum certification and is waiting on confirmation from USGBC.
System Upgrades
Chris Horch took control of the PowerPoint and transitioned from full building renovations to system upgrades. He explained that owners might not have the budget to renovate an entire building and that is when good operators prioritize the replacement of aging infrastructure, such as heating and cooling. Chris got into the specifics of a $2 million capex project for a confidential client – a 200,000 s/f commercial building.
As part of the capital improvements, they replaced – the steam absorbers with electric drive chillers – the steam systems with high efficiency gas boilers – and two 350-ton chillers with modular chillers. Horch reviewed many advantages of the investment, detailing that this project had a conservative ROI of 5.4 years.
SIMPLE STROKES – HIGH IMPACT
After spending time on big ticket budget and timeline initiatives, Chris specified that owners don’t always have to go big. As it relates to energy savings and tenant comfort, every operator has the ability to retrofit floors as they become available. Chris said that there are many simple things that owners can do that will still have high impact.
He disclosed that RXR, owner and operator of the Starrett Lehigh Building, placed wireless radiator dials that operate on Wi-Fi and do not require batteries, as well as VAV boxes for induction units throughout the entire 2.4 million square foot building. This netted an 18% reduction in gas usage.
Tune the Loops
Ryan Lean brought the presentation back to basics and reviewed the importance of tuning the systems in place. As a general rule, Ryan recommended to first test individual components to correct the issues locally before assessing the entire macro system. He also talked about conducting thoughtful airflow accounting, in order to find the ideal formula to achieve the expected CFM in all spaces of a building.
He stressed that “data” is imperative and explained that the entire sequence of operations is based on the information provided to the building management system. For example, he justified that all of the captured information controls how valves are responding and how dampers are opening and economizing.
Particularly with larger buildings, as we manage them and fix daily issues, we forget to tune. Ryan said that it’s important to spend the time to bring systems back from where they drifted from. He referenced the Brooklyn Museum and the importance of maintaining the climate (temperature and humidity) for the many pieces of art and artifacts in that building. As an example, he alluded to humidity sensors and asked the room how often they have to be recalibrated. The answer – once per year. His message – know your facts.
Intro: Bill 1253
At the conclusion of the case studies and many best practices to upgrading aging building infrastructure, the JB&B trio provided a brief overview of Bill 1253 – the most significant and unprecedented piece of legislation for the built environment. The goal is a citywide 80% reduction of greenhouse gas emissions by 2050. Noncompliance will be faced with major fines, beginning as early as 2024.
They explained that the Bill has enough votes to pass right now and anticipate that the bill will be approved on Earth Day, April 22, 2019 (side note –Bill 1253 was approved on April 18, 2019). Now is the time to operate right, begin fine tuning, research utility rebates and springboard a system wide costs benefit analysis.
Building Owners & Managers Association of Greater New York (BOMA NY) is the largest local association in the BOMA International federation, which represents commercial real estate responsible for the ownership and management of some of the world’s most prestigious properties. BOMA NY serves as the first line of defense for New York’s working public, accountable for the safety, physical well-being and security of the City’s 3 million office tenants. For more information about the Association and/or have any questions, please call the BOMA NY office at 212-239-3662, or visit its website – bomany.org.
UPCOMING BOMA NY EVENTS:
May 1st |
LEED AP O&M Exam Prep |
May 2nd |
Register for the LEED Green Associate Exam Prep |
May 9th |
Energy Action Day – The First Seminar About Bill 1253 |
May 15th |
Wine Tasting at State Grill & Bar |
May 16th |
Lunch and Learn – It’s Electric! |
May 20th -22nd |
BOMI: Accelerated Course – Asset Management |
June 10th |
Golf Classic at Edgewood Country Club |