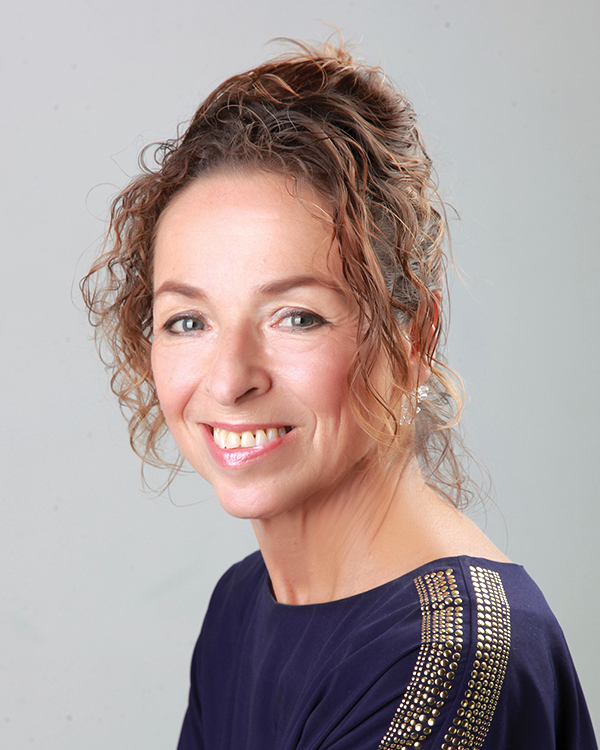
Tyga-Box Systems
Borrowing a statistic from global manufacturing operations, production equipment is utilized 52% of the time with the balance of 48% of time being lost in maintenance, upgrades, shutdowns, etc. resulting in reduced asset productivity and Return on Assets (RoA).
Similarly, underutilization concerns apply to oil and gas companies who refer to asset underutilization as Non Production Time (NPT).
Likewise, in rail cars and freight containers, measured using Asset Performance Management (APM) metrics, reveal utilization to help avoid unnecessary negative impacts to the bottom line.
So how is furniture fixtures and equipment (FFE) utilization captured, measured, managed and optimized?
Our industry challenges are similar to the industries cited above in that what’s necessary to define the metrics which will help increase asset utilization is to aggregate massive quantities of structured and unstructured data.
Where we differ meaningfully is that a significant percentage of the asset pool is (a) highly mobile (e.g. chairs), (b) low value compared to asset values in other industries, (c) distributed throughout interior premises, making them difficult to locate, (d) have depreciation schedules commonly ranging between 5-10 years.
According to a CBRE report: “North America Occupiers’ Fit-Out Cost Guide” 2015 FFE comprises 29.3% of average office cost per s/f, with workstations (and all those chairs) comprise approximately 70% of space plan usage.
The challenge is that they’re mobile assets which are repositioned several times a day, a week, or a year by myriad unknown parties to myriad unspecified, unrecorded locations.
The irony is that these moveable assets belong to a fixed asset classification, and are categorized as a long-term asset. Verification of their physical presence through the end of their respective depreciation schedules must be made on an annual basis in order to tie out the balance sheet.
The current process of manually accounting for these mobile, low-value assets is time-consuming, reasonably inaccurate and absolutely essential to be in compliance with government authorities.
Adapting asset tracking best practices from other industries, combined with innovative mobile RFID item tracking solutions specifically engineered to meet the needs of todays’ workspaces, could solve both the accounting requirements and at the same time increase utilization efficiencies at prices commensurate with asset value.
The Internet of Things (IoT) is a known catalyst for asset tracking and transforming business processes by using real-time data in automated, accountable and transparent ways. Asset utilization can now be identified, predicted and prescribed thusly.
The IoT is growing to meet the needs of leaders who desire to transform their businesses as evidenced by IBM’s “Watson IoT Platform,” intended to become the hub of enterprise IoT, complete with integrated solution providers and applications, and Microsoft’s recent launch of IoT Central, a fully managed “IoT-as-a-service” offering to assist enterprises with the deployment of IoT applications without the need for in-house expertise.
Current IoT data-collection tools lag behind the vision of the IoT, and rely heavily on models from “yesterday:” (a) cost borne by single user, (b) site surveys required, (c) permanent installations, (d) fixed position gateways and (e) use of barcode readers. These “yesterday” tools such as barcode readers may be a good fit to track items which generally remain in a fixed position such as servers and pumps, however, they are a relatively poor fit for providing security, tracking, and utilization data for mobile FFE assets such as the kinds you tend to see in today’s mobile, flexible, multi-purpose workspaces which self-assemble into multi-functions decided upon in real-time by spontaneous, creative co-workers.
What’s needed for the IoT to fulfill its potential, and for parties responsible for keeping track of FFE assets, are new data-collection tools that drive data collection down to the lowest level of competence and fully automate the process so that no human intervention is required. Although we all love humans, they’ve been known to vary in performance with respect to the quality of data collection, vacillating between accurate and inaccurate, and unpredictably so!
Breakthroughs in data-collection tools will prompt us to re-think what’s possible and re-tool the workplace with self-assembling networks of mobile assets, mobile people and mobile hardware. It’s in this type of networked, automated mobile environment that we can fulfill our responsibilities as stewards of mobile FFE assets, and have the confidence that our data is absolutely accurate.
At the foreground of these automated breakthrough technologies is TygaTrax – security and tracking for any item, anytime, anywhere, on a completely mobile, scan-free, hands-free basis.
Nadine Cino, LEED AP, is the CEO and co-Inventor of Tyga Technologies Inc, and Tyga-Box Systems, Inc., New York, N.Y.