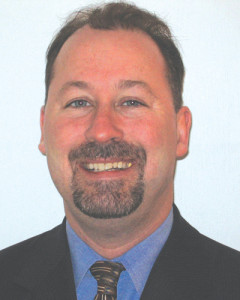
Chuck Merritt, Merritt Environmental Consulting Corp.
When the American Society of Testing Materials (ASTM) released the ASTM E-1527-13 standard in the fall of 2013 there was greater emphasis placed on including the potential for a Vapor Encroachment Condition (VEC) to exist at a property. Vapor Encroachment is the process by which contaminants breakdown and volatize into a gas. These vapors can travel more freely then contaminants attached to the soil or floating in the groundwater. The ASTM standard included some direction on how a consultant can determine if this condition may exist. This “direction” includes evaluating the property and adjoining properties within a certain distance of the subject site. The most common culprits for causing such a condition are solvents that are typically used at industrial/manufacturing sites, dry-cleaning establishments as well as sites storing gasoline and other petroleum products. When the potential for a VEC has been established, it is to be reported in the Recognized Environmental Condition (REC) section of the phase one report.
There are a few methods in determining if vapors are present at a site which can be deployed individually or in concert with each other. This typically includes sampling of the soil, and groundwater and normally takes place within a phase two investigation. Obtaining samples of the soil and groundwater and sending to a laboratory can assist in determining if an impact is present. The other methodology gaining traction of the last several years is conducting a soil gas vapor survey. This approach of testing all media’s in which contaminants can travel at a site is also the most costly.
The reason for vetting if vapor encroachment may be present at a site is to ultimately determine if a Vapor Intrusion Condition (VIC) exists inside a structure. This condition occurs when the migration of hazardous vapors from contaminated soil or groundwater enter through cracks in the building foundation into overlying buildings. Exposure to these vapors can pose potential health risks to the building occupants.
Earlier this year, the United States. Environmental Protection Agency (USEPA) updated its recommendations for identifying, evaluating and managing vapor intrusion. The recommendations were published in two documents “Technical Guide for Assessing and Mitigating the Vapor Intrusion Pathway from Subsurface Vapor Sources to Indoor Air” and “Technical Guide for Addressing Petroleum Vapor Intrusion at Leaking Underground Storage Tank Sites,” both released in June. The former was developed to address vapor intrusion at a wide variety of sites with a broad range of contaminants. The latter is specifically designed for sites with petroleum contamination from underground storage tanks (USTs), which are typically characterized by small release volumes and the potential for natural degradation of contaminants.
These publications are considered guidance documents, which EPA issues to assist the public and regulated entities, as opposed to legally enforceable laws and regulations. EPA took into consideration updated toxicity values, recent case studies, and improved mitigation techniques in compiling the guides. The new documents contain a greater amount of information regarding commercial and industrial sites than the previous guidance, which was primarily intended for use in residential settings. These are the first vapor intrusion guidance documents to be released by EPA since 2002. In the interim, most states had developed their own guidance or regulations to address vapor intrusion, and the states are now looking to update their regulations in light of the new federal guidance.
The New York State Department of Health (NYSDOH) currently uses its own guidance document which was issued in 2006 and more stringent in many respects than the federal version so it is important to understand what may be required once testing is conducted and elevated levels are determined to be present. Consultants and their clients should discuss these “next steps” prior to the investigation as additional testing will cost additional time and money.
Once vapor intrusion is known to be a concern at a site, the condition can be mitigated through relatively simple actions, such as changing building pressure and ventilation. This measure can be deployed during new construction as the excavation of a site lends itself to the installation of mitigation systems more easily. Retrofitting existing buildings that have a vapor issue can be a bit more challenging as the working conditions can be more constrained.
The new guidance document is available at: http://www2.epa.gov/vaporintrusion
Chuck Merritt, LEED AP, is the president of Merritt Environmental Consulting Corp., Hauppauge, N.Y.