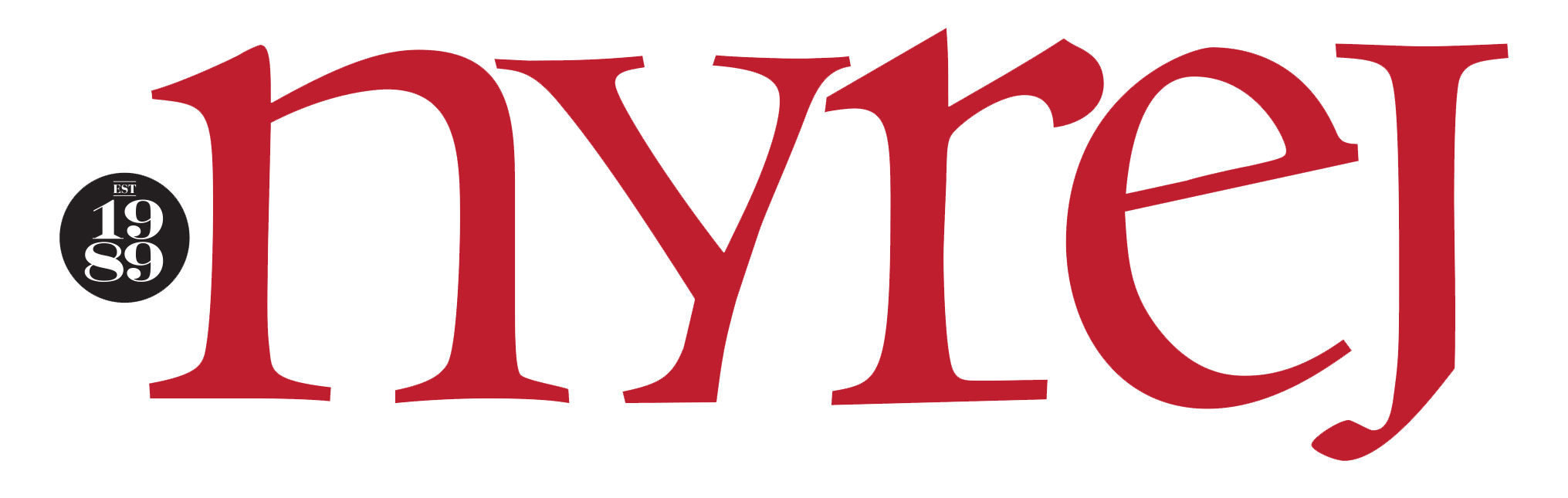
May 13, 2013 -
Long Island
Circa 1970, the U.S. was going through a challenging economic period, however, U.S. manufacturing was still king of the world - flexing its muscles as a manufacturing power house. Detroit was untouchable, manufactured imports were not a concern, and there were no emerging markets.
It began with foreign imports of cars and how Toyotas and Hondas were exceeding reliability and quality standards of U.S.-made automobiles. Next came the steel industry, and slowly but surely began the erosion of our manufacturing base. It became worse with the enactment of NAFTA which sent our manufacturing jobs over the border into Mexico.
Fast forward and China and India emerged as low cost manufacturing countries, producing and exporting goods at every level of the retail market, at a cost far less than U.S. manufacturers could meet. It was only a matter of time before the emerging markets were going to start losing their status as the number one place to manufacture your goods. Suddenly, the issues started to surface. Their employees were becoming more westernized, demanding higher wages and looking for better working conditions. In addition, product quality control was deteriorating and export shipping costs were rising. Furthermore, and not to mention, substandard electrical grids and rolling power blackouts were interfering with U.S. companies and their schedules with their vendors.
Suddenly, U.S. manufacturing companies started to rethink and calculated that the savings were not as much as before. Slowly, multinational companies are retooling and firing up their U.S. plants. There are many examples of the import of substandard products; most notably, the housing expansion in the south and south west where builders were importing sheet rock from China. Over a period of time, the sheet rock started to sweat toxic chemicals. New homes had to be evacuated and completely renovated to the cost of approximately $125,000 per home.
Another prime example is the manufacturing of health care products. The health care industry has experienced the same issues with manufacturing in emerging markets. Initially, the prognosis was good with low costs and effective quality control, but as time went on, the advantages started to wane.
Now, they are finding it is less expensive and of far better quality to manufacture in the U.S. In one case, an Indiana-based company, decided to expand its manufacturing base in New York and add 400 new jobs. Part of the answer is a more educated work force. The governments of emerging markets are another problem. Corruption is commonplace that adds to the complexity of the matter, getting the job done.
Another factor that is helping the flight of manufacturing back to the U.S. is the cooperation of unions. In addition, the emerging markets do not have the same environmental quality control standards as exist in the U.S., as evidenced by the shoddy Chinese sheet rock example previously cited. Recently, it was brought to my attention that a manufacturer/importer of the apparel products were now having their apparel randomly tested by their customers (i.e., department stores) for environmentally-sensitive materials.
Another boost for manufacturing is the assistance of government-sponsored programs to help build our manufacturing base. With all this being said, I said many years ago that it would only be a matter of time before the U.S. manufacturer would say, "There is no place like home." In March, The Institute of Supply Management reported that U.S. manufacturing activity continued to expand in March. That was the fourth straight month of growth. According to the financial data firm, Markit, U.S. manufacturing also posted its best quarter in two years. Stay tuned...
Ralph Perna is an executive managing director at Newmark Grubb Knight Frank, Melville, N.Y.