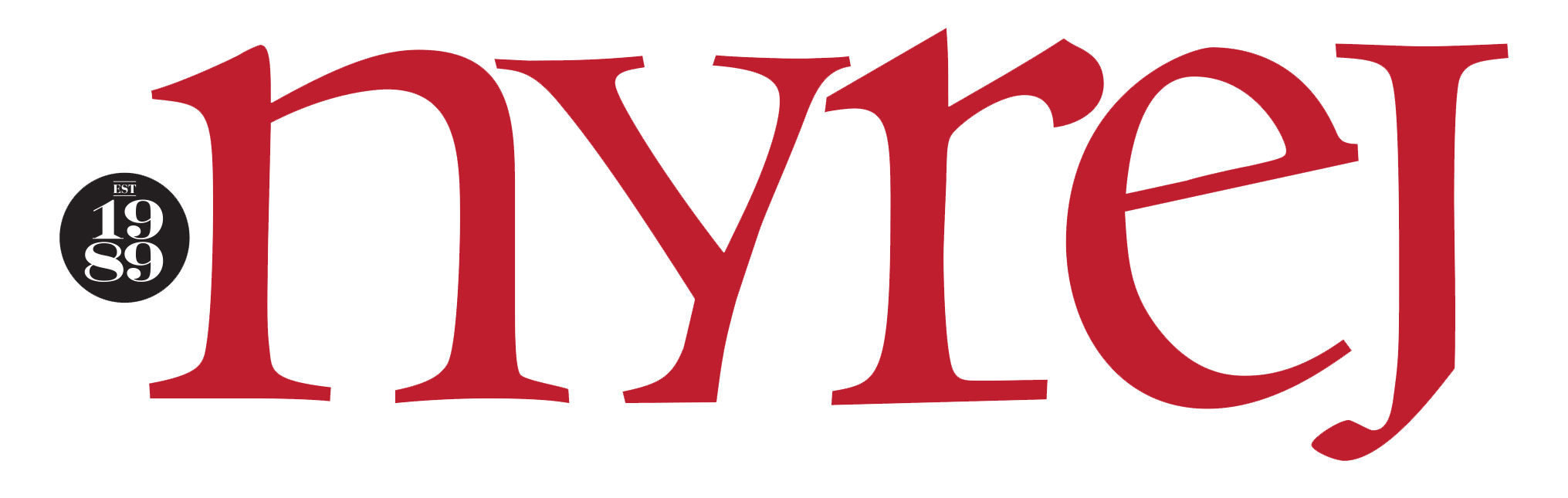
Any discussion of building safety is likely to include subjects such as: building egress in the event of fire or power outage, personal security within the building and on its grounds, and procedures relating to building maintenance and repair.
A discussion of building safety may also include environmental issues affecting building occupants, such as lighting, ventilation, and even the selection of cleaning materials to minimize solvents and other chemicals that may cause allergic reactions.
However, the selection of construction materials used in retrofit applications can also be of paramount importance. Many construction materials contain solvents, formaldehyde, and other volatile materials. These materials can become airborne and enter the air handling system and thus spread quickly throughout the building.
Waterproofing upgrades are common retrofit activities, both exterior to the building on roofs, plazas, and terraces, as well as within the building's interior in mechanical rooms, loading docks and parking garages.
A new class of waterproofing materials are available that provide excellent waterproofing performance, at the same time eliminating solvents and other volatile organic compounds (VOC). These cold, reinforced liquid-applied materials are typically urethane-based products that utilize two-component, reactive-cure technology.
Briefly, cold liquid-applied reinforced membranes are by nature fully adhered systems. In their simplest form, cold liquid-applied membrane waterproofing systems consist of a reinforcing fabric saturated in the field with a liquid polymeric resin. The reinforcing fabric is cut to fit the contours of the substrate and penetrations, resulting in a close-fitting membrane and flashing system.
Cold liquid-applied membrane systems are monolithic, seamless, and conform to nearly all configurations. The reinforced liquid resin membrane systems fully adhere directly to practically any structural surface (horizontal or vertical), thereby preventing water migration behind and beneath the waterproofing membrane
Some cold liquid-applied waterproofing manufacturers have begun using odorless, non-toxic, solvent-free, environmentally safe products because of the costs associated with disrupting business operations. Many times the project includes working near air duct systems where foul smell and toxicity can be a concern. Building tenants are becoming more and more sensitive to anything that suggests a possible threat to their health. Cold liquid-applied membrane systems are available with a VOC level less than 10 g/L—which is significantly lower than the standard maximum VOC level for roofing adhesives and coatings of 200 to 250 g/L.
As a related consequence to this focus on non-hazardous, environmentally safe products, a growing trend among manufacturers is the use of more renewable raw materials in their products. For example, many systems now substitute manufactured petroleum oils with oils from plants such as sunflowers. In addition, recycled or reclaimed polyester or fiberglass fibers can be used in the reinforcement fleece embedded in many waterproofing and roofing membranes.
Kemper System Inc., a worldwide manufacturer of reinforced cold-liquid applied waterproofing and roofing membranes, manufactures an odorless, environmentally-friendly product that has been used for years on high-profile projects in New York City as well as nationwide.
7 World Trade Center Mechanical Room
A newly constructed mechanical room on the 20th floor at 7 World Trade Center where extensive new construction took place in a rebuilding phase in 2005, used odorless, Kemperol 2K-PUR waterproofing membrane to seal an area populated with multiple mechanical units. The presence of the machinery was a concern as it might cause future leaks and damage to valuable occupied space below.
"This saved a lot of time and money by not having to close down business activities in the immediate project area," said Brian Kelly, Kemper New York regional sales manager. "They had a lot of people working nearby and odorless, solvent-free and non-toxic were mandatory elements in the waterproofing system the owners required."
Federal Reserve Bank Main Roof
While Kemperol materials had already been installed on several waterproofing and roofing projects at the Federal Reserve Bank of New York City, 2005 marked the first application of odorless Kemperol 2K-PUR membrane to the main roof. The building's old asphalt roofing system had reached its life expectancy, experiencing multiple leaks and causing costly damage to the large governmental financial institution.
The old roofing system was removed and a new waterproofing system installed, over which was placed a quarry tile overburden. The new waterproofing system readily accommodated the multiple irregular flashings located throughout the roof.
"Another concern was the air duct system, which was built directly into the roof and could not be shut down, so odorless and non-toxic became huge issues that we were able to address 100%," said Kelly.
Weill Cornell Ambulance Entrance Drive
Weill Cornell Medical Center is a nationally-renowned medical facility, and provides critical medical services to New York City residents. The facility's ambulance entrance drive is located directly over occupied space. Over time, the original concrete slab developed leaks, and the installation of a new waterproofing membrane and traffic-resistant surfacing was indicated. Because the entrance drive passed through the building, it was protected from direct precipitation. However, increasing traffic volume resulted in significant rain water, melting snow and ice being brought into the drive area.
Because the ambulance entrance drive was located within the building, and sensitivity to health-related issues could not be of greater importance, the use of an odorless system was mandated. A system consisting of Kemperol 2K-PUR membrane and TC urethane-based, mineral-filled traffic coating with an aggregate finish was installed.
These projects clearly illustrate the advantages of cold liquid-applied reinforced membrane systems. Waterproofing technology has certainly come a long way since the days of fuming hot asphalt kettles and noxious solvent-based coatings.
Paul Allenstein is the technical director of Kemper System, Inc., Teaneck, N.J.