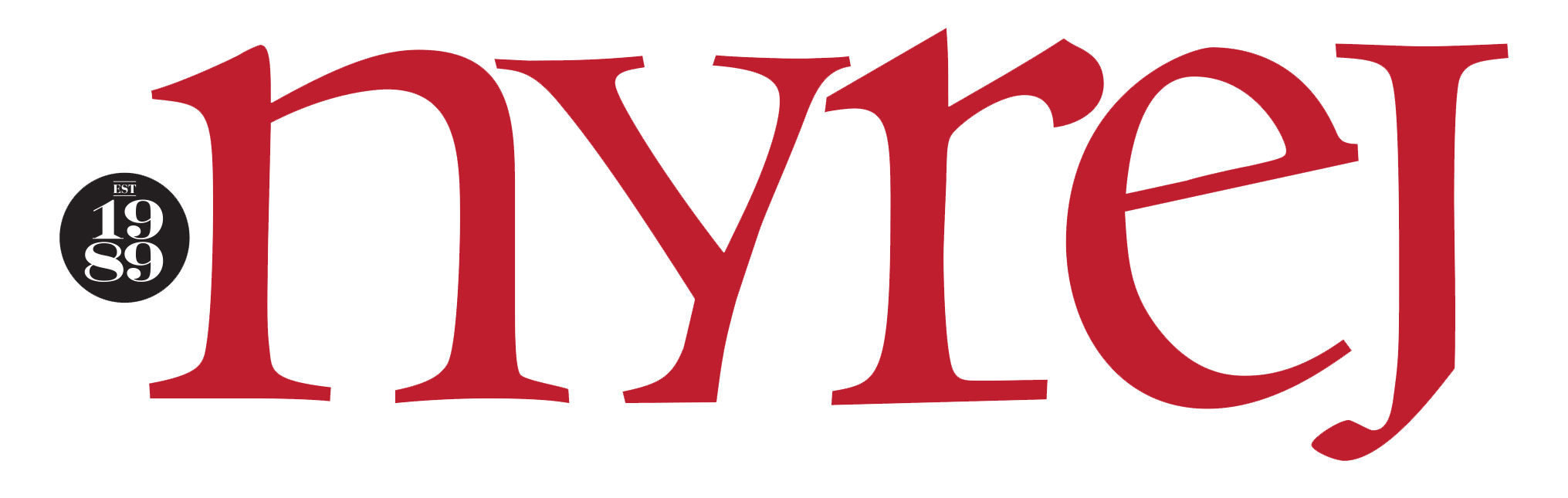
September 26, 2011 -
Green Buildings
Providing both capital and collaboration, GE led a $22 million investment round in Project Frog and began construction on one of its prefabricated environmentally sustainable buildings at GE's John F. Welch Leadership Development Center.
Led by GE unit GE Energy Financial Services and joined by other investors including Claremont Creek Ventures, Greener Capital Partners and RockPort Capital Partners, the $22 million investment will help Project Frog expand its sales pipeline and execute orders.
Construction of the Project Frog building at GE's John F. Welch Leadership Development Center is expected to be completed by the end of this year.
Established in 1956, the Learning Center, also known as "Crotonville," was the first of its kind and has been at the forefront of real-world application for the latest thinking in organizational development, leadership, innovation and change. Construction of the Project Frog building is part of a broader venture that is aimed at rethinking Crotonville to support 21st century learning by embedding new attributes to the curriculum, redesigning facilities and empowering participants to own their own learning experience. GE is committed to pursuing LEED certification - an internationally-recognized green building certification system developed by the US Green Building Council - for select buildings at Crotonville.
Project Frog fills a market need for high-quality, energy-efficient buildings at a lower cost and less time to completion, which our investment and collaboration will help demonstrate," said Ricardo Angel, senior vice president of venture capital at GE Energy Financial Services.
Project Frog's technology improves traditional building construction methods by combining semi-custom designs with a pre-engineered kit of energy-efficient building components. This enables higher quality, more environmentally sustainable, faster and cheaper construction. Through advanced performance modeling, Project Frog analyzes how its buildings will perform in each location, allowing owners to optimize a building kit to match their desired performance. The kits are delivered to project sites ready for assembly, and typically take one to six months to construct —less than half the time required for traditional construction. Project Frog's buildings use at least 25%less energy than the strictest building codes in the United States, and as much as 80% less energy in certain parts of the country. Project Frog manufactures its commercial building systems for educational and government organizations, healthcare offices and retail spaces.
"We make the complicated and lengthy process of new construction faster and easier for our customers by providing a kit of high precision, sustainable parts that are optimized based on the structure's size, use and location," said Ann Hand, CEO of Project Frog.